How New Zealand’s Wineries Can Preserve Soil Quality and Sustainability in Their Pursuit
of World-Class Wines
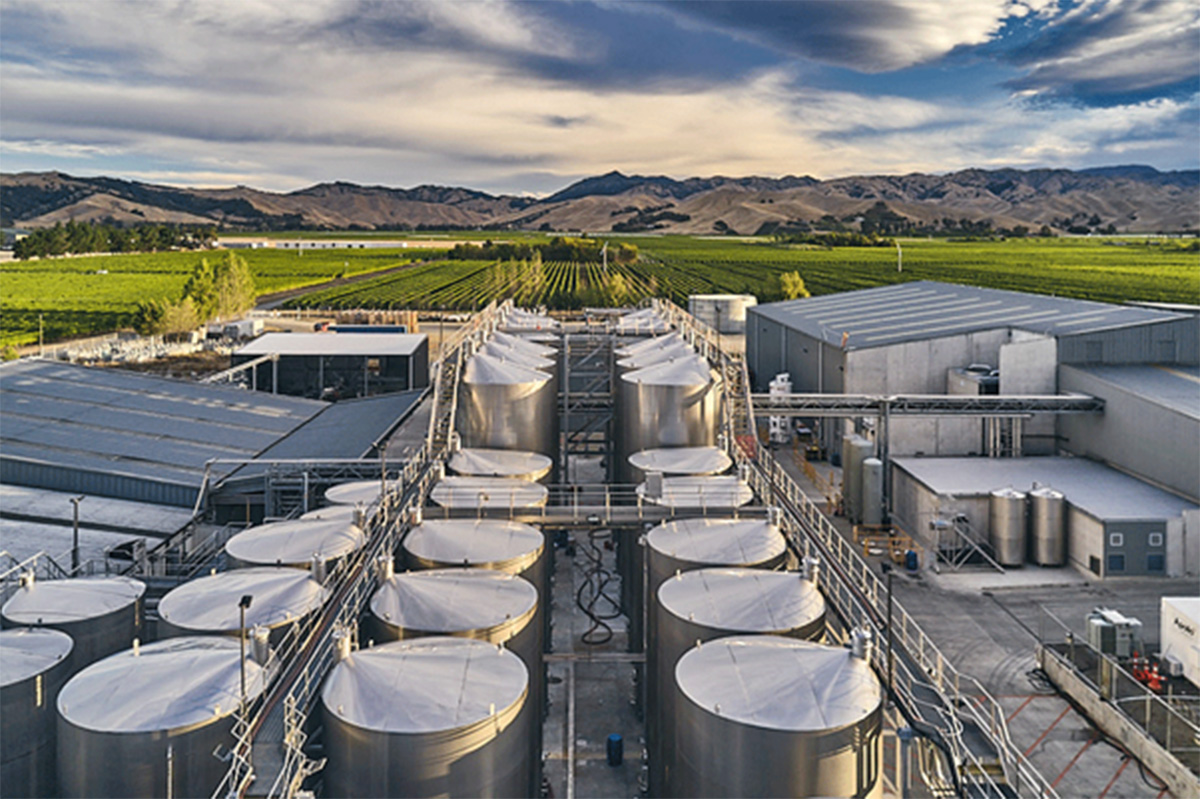
Introduction
Over the past two decades, Marlborough’s wine industry has experienced significant expansion, with the region producing approximately 268 million litres of wine in 2022. Remarkably, for every litre of wine, an estimated 10 litres of wastewater is generated, totalling 2.68 billion litres of wastewater annually. Faced with this ecological challenge, many wineries have adopted wastewater recycling for irrigation on their vineyards and adjacent land. However, emerging evidence suggests that this practice may negatively impact soil quality, potentially jeopardizing the region’s long-term viticultural sustainability.
The Sodium Hydroxide Predicament
Wineries around the globe rely heavily on Sodium hydroxide for pH control in their wastewater treatment processes. This chemical has indeed proven effective, but it comes with a set of unanticipated consequences. One of the most troublesome side effects is the escalation of soil sodium levels, typically quantified by the Sodium Adsorption Ratio (SAR). Sodium, as a monovalent ion, infiltrates the soil, impairing its macroporosity, a hindrance to root growth that restricts water and air movement within the soil structure.
The high SAR values of irrigated land caused by using Sodium Hydroxide for pH control and in cleaning processes raises a sustainability challenge for wineries in the future.
Potassium hydroxide is often raised as a preferable alternative for mitigating sodium loadings. However, being another monovalent ion, potassium can also exacerbate soil structure issues, albeit to a lesser extent. So what can be done?
The Magnesium Hydroxide Solution
When manufactured correctly, Magnesium Hydroxide can be used as an alternative to Sodium and Potassium Hydroxide for pH control in winery wastewater treatment. Not only does this prevent future addition of Sodium or Potassium to soils, it actually helps reverse accumulation. Magnesium is a divalent ion, and easily exchanges with Sodium and Potassium in the soil, thereby lowering SAR and PAR (Potassium Adsorption Ratio).
The relative obscurity of Magnesium Hydroxide is partly due to its low solubility in water, a hurdle that technological advancements have recently overcome. Improved calcination methods for the raw material, Magnesium Oxide (MgO), and innovative hydration techniques have rendered stable and reactive liquid forms of Magnesium Hydroxide feasible.
As a pH control agent, Magnesium Hydroxide Liquid (MHL) often performs better than Sodium or Potassium Hydroxide. Less MgOH2 (60%) liquid is needed vs 50% sodium hydroxide to neutralise acidic wastewater, making it cheaper than Sodium and Potassium Hydroxides.
As a pH control agent, Magnesium Hydroxide Liquid (MHL) often outperforms sodium or potassium hydroxide, with less MHL required than Sodium Hydroxide on an equivalent basis for neutralizing acidic wastewater, making it a more cost-effective choice. Perhaps its most alluring quality, however, is its safety profile; MHL is practically non-hazardous, with its pH peaking at around 10.5 and low solubility rendering it safe to handle. As a testament to its benign nature, Magnesium Hydroxide is utilized in over-the-counter remedies like “Milk of Magnesia” to alleviate heartburn.
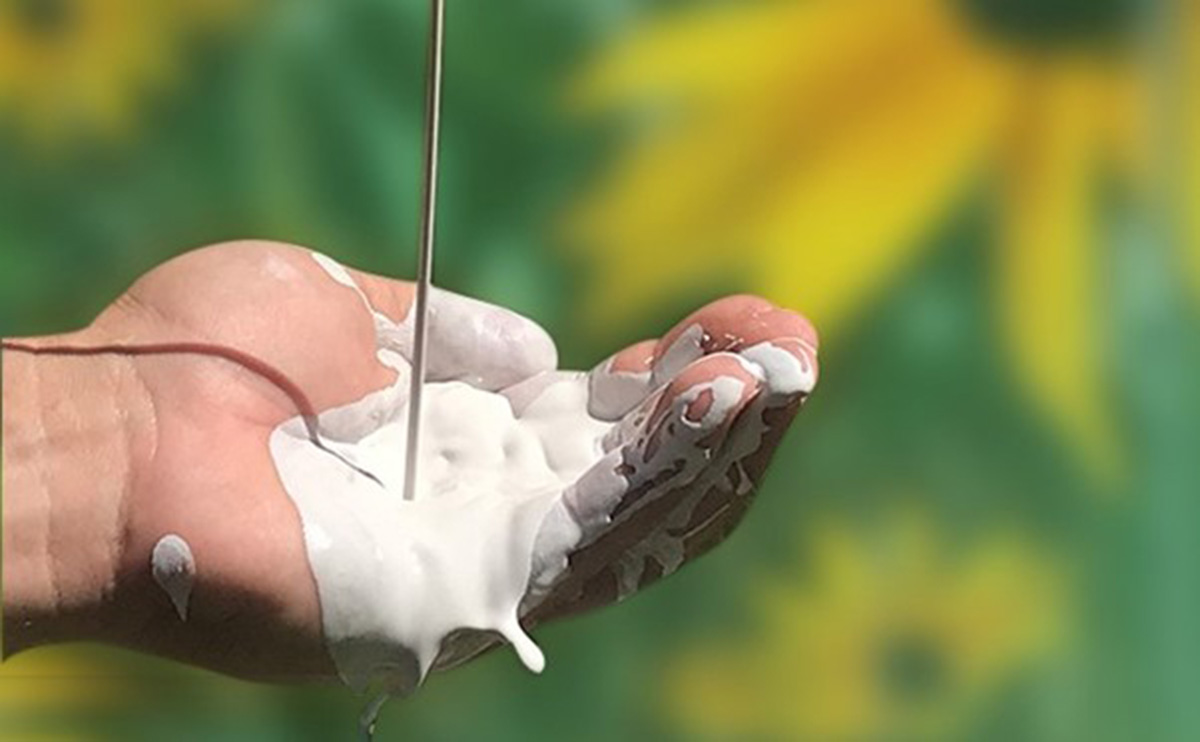
Making the Switch – Not all MHL is the same
Parklink’s Magnesium Hydroxide Liquid stands out as an exemplar of quality and reliability. Its high stability and reactivity means it can usually be swapped out directly in winery pH control systems, something previously not possible. Moreover, it boasts competitive pricing, making it the most economical choice on the market.
To delve deeper into the product’s potential benefits, contact Parklink today at info@parklink.co.nz.